Blog
Essentials in today’s LNG market
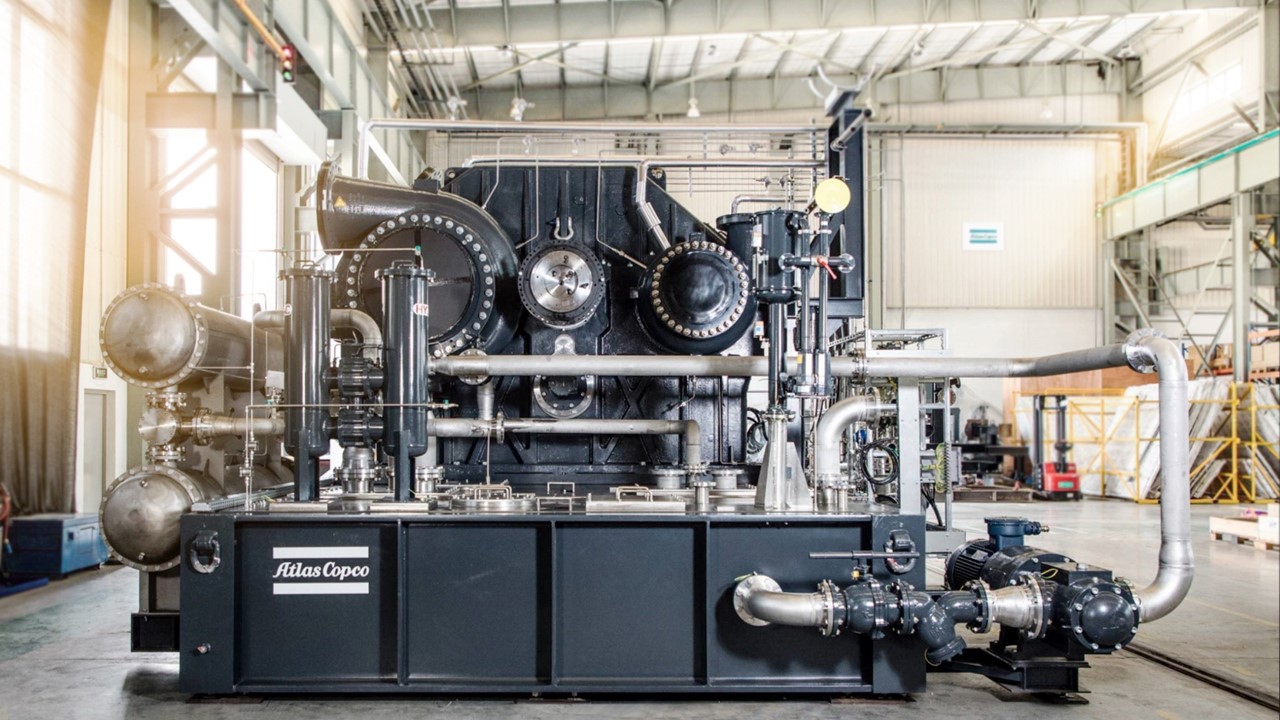
"COMPRESSOR RELIABILITY AND EFFICIENCY ARE ESSENTIAL IN TODAY'S LNG MARKET"
In this interview, Nick Leaf and Michael Drewes from Atlas Copco Gas and Process discuss current trends and drivers in gas compression equipment serving the global LNG market. Leaf oversees the market segment Carrier LNG (CLNG), while Drewes is responsible for Small-Scale LNG (SSLNG).
Atlas Copco Gas and Process has a rich history in serving the LNG market. What are some milestones?
Leaf: Our history in LNG now spans five decades. It includes many proud milestones such as the onboard reliquefaction systems using our Compander or, more recently, the introduction of our oil-free screw technology for BOG management on LNG carriers and for LNG fuel systems.
Drewes: In the arena of small-scale LNG, one major milestone was the recent commissioning of the world’s largest integrally geared mixed refrigerant compressor in China, a 27 MW unit.
Which areas of LNG are you currently active in?
Leaf: For offshore, the main areas are CLNG, LNG as a fuel, and FLNG. We serve CLNG with high-duty and low-duty integrally-geared centrifugal compressors, and gas screw compressors. In reliquefaction applications, our Compander – which combines compressor and expander functionality in a compact unit – is often used.
Drewes: For land-based applications, we supply turbocompressors and expanders as well as the Compander for different refrigeration cycles like the Brayton (N2) cycle, the Mixed Refrigerant cycle as well as the Methane cycle. Vapor Return Blowers and BOG compressors also belong to our portfolio.
When you engage with your customers, what are some of the key operational requirements for them and what are some of the main advantages integrally-geared technology brings to the LNG market?
Leaf: When talking to ship owners, reliability and OPEX are the key aspects. These customers are often running charters for 20 years. That means they need to have long maintenance intervals, and maintenance is a challenge. Therefore, they need our compression equipment to run reliably – we meet that requirement. On the carrier side specifically, I want to add that integrally-geared compressors are oil-free, as compared to some other compression technologies. This is a key aspect on carrier ships, for example in boil-off gas reliquefaction processes.
Drewes: In SSLNG, things also boil down to low CAPEX, high reliability, as well as low OPEX. Important customer “pressure points” include best energy efficiency, lowest seal leakage rates, smallest footprint, as well as long maintenance intervals combined with ease of maintenance. Operationally, high turndown rates and wide rangeability make integrally-geared a very viable choice for customers.
Additional options for you:
- find out more about International LNG Congress at lngcongress.com
- request marketing materials here
- share the article in your social network using the buttons below and our tag #LNGCongress2020